Wood chip press!
Mechanical drying
What are your goals? What requirements do you want to solve? Let’s make it concrete together.
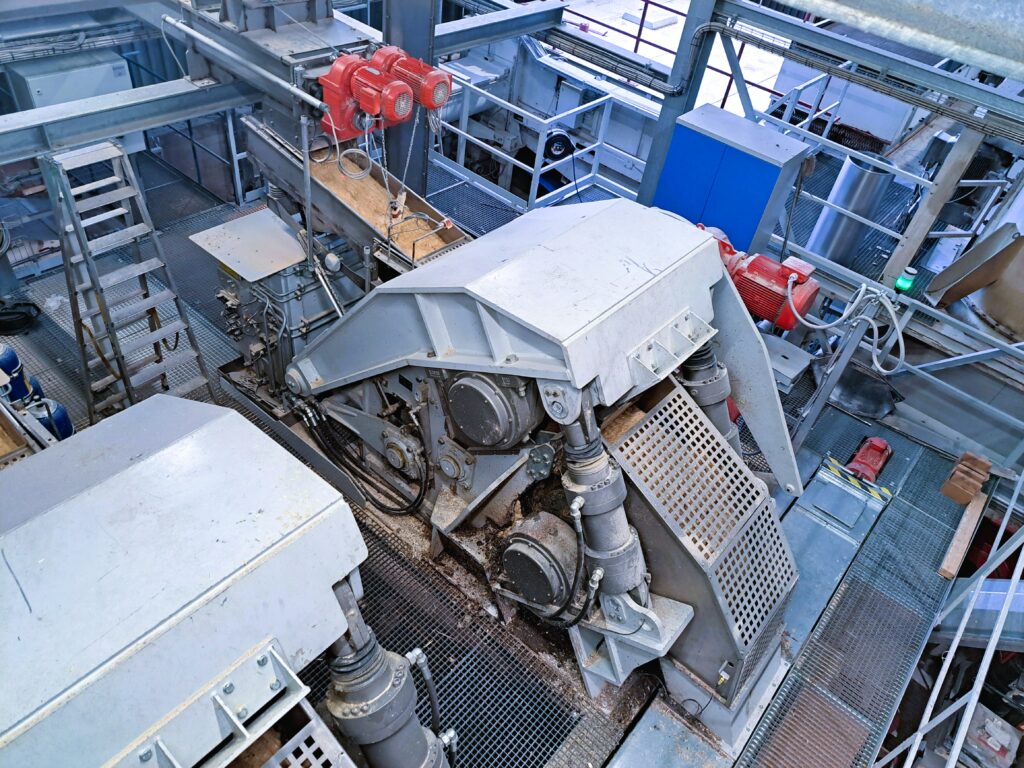
Mechanical drying
of
Wood chips or residual wood waste
With our cross-sector know-how in the wood industry and our experience in hydraulics and mechatronics, we will soon create your individual system. Productive, efficient, profitable. Tailored precisely to your requirements.
Your advantages
Energy saving
With around one kilowatt hour of mechanical energy, more than 70 liters of water are pressed out of the wood chips. Conventional systems with classic hot air drying require 1.7 kWh electrically and 90 kWh thermally!
Constant residual moisture
A large proportion of the free water that is not bound in the cell wall is removed mechanically. This results in a residual moisture content of 35%-38%. This makes the subsequent belt drying process more efficient and economical.
More efficient transportation
If half of the water disappears directly at the factory, a quarter of the weight of the woodchippings also disappears – and a superfluous quarter at that. This immediately saves on transportation costs.
At Neuson Hydrotec, know-how and components merge into systems with a functional design. Elegant and efficient solutions for complex requirements – for your market advantage.
Find out more about our expertise
Send us your requirements in 4 short steps and book your consultation today.
Technical data:
Roller width: | 510 mm |
Pressing force: | 1000 kN |
Press pressure: | 300-400 bar |
Throughput: | 20 -30 srm/h (bulk cubic meters) |
Reduction of the water content: | Initial content 52-63% to final content ~35 % |
Weight of the unit: | approx. 17 to. (without feed and discharge) |
Motor power: | 2 x 22 kW |
Typical power consumption in continuous operation: | approx. 30 kW |
Footprint of the unit: | approx. 3 x 4 m (without inlet and outlet) |
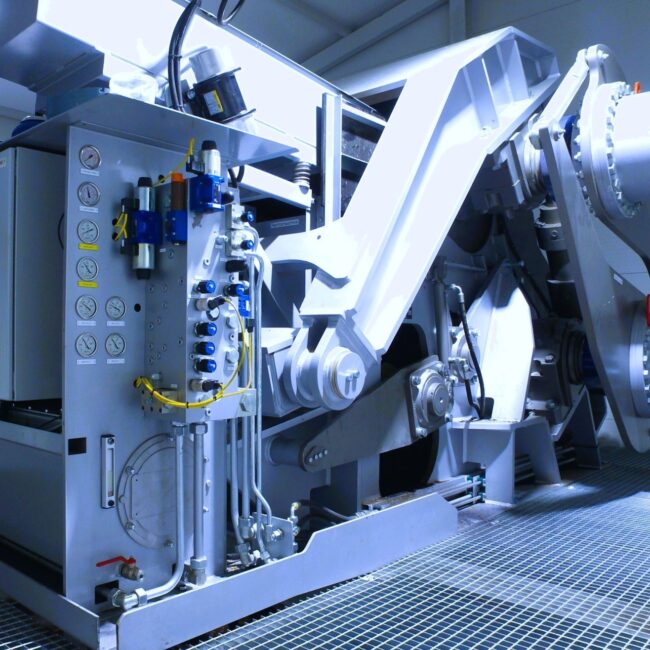
Customized installation
We take things into consideration! Depending on the local conditions, we can also supply the steel substructure and platforms if required.
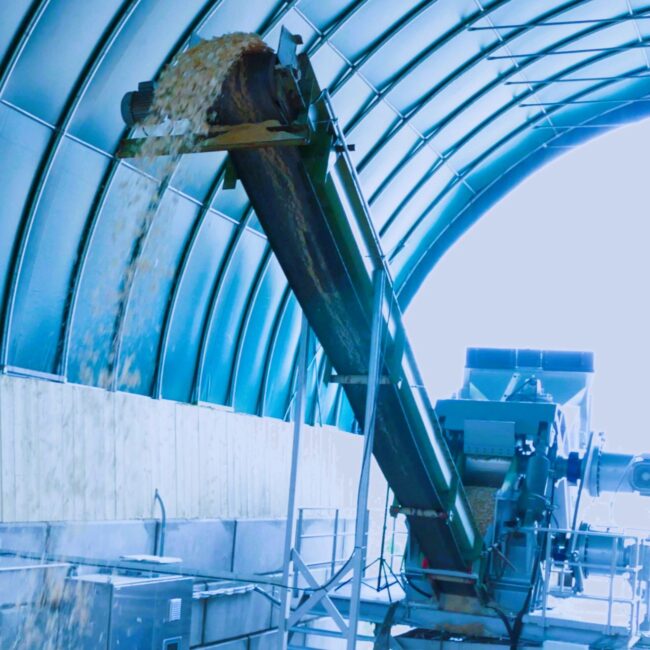
Conveyor technology
With decades of experience in conveyor technology, we supply the supply and removal of woodchippings, taking into account the on-site systems.
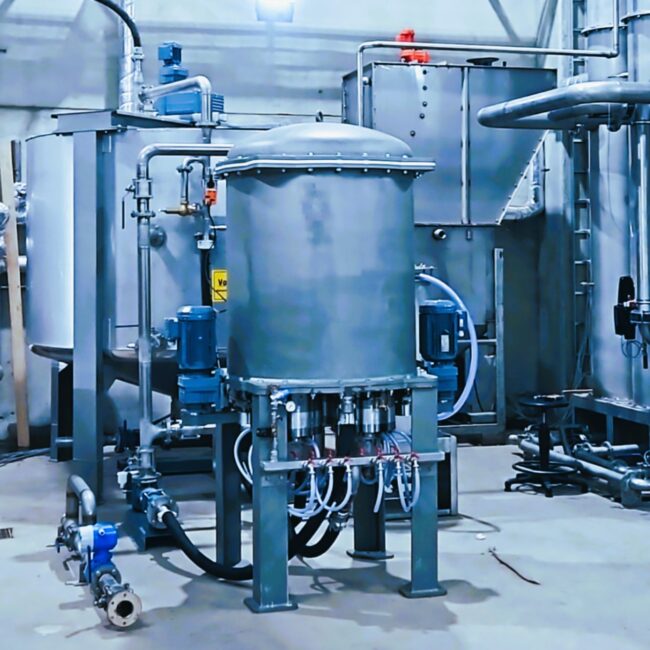
Water treatment
Depending on the local guidelines for the discharge of waste water, we work with our partner to develop a concept or a system for water treatment.
Selected references
Baltic Block
The Baltic company in Latvia produces pressed wood parts for pallets in 24-hour operation. In order to optimize the overall process in terms of the energy balance and at the same time significantly increase throughput, two wood chip presses were integrated into the existing process
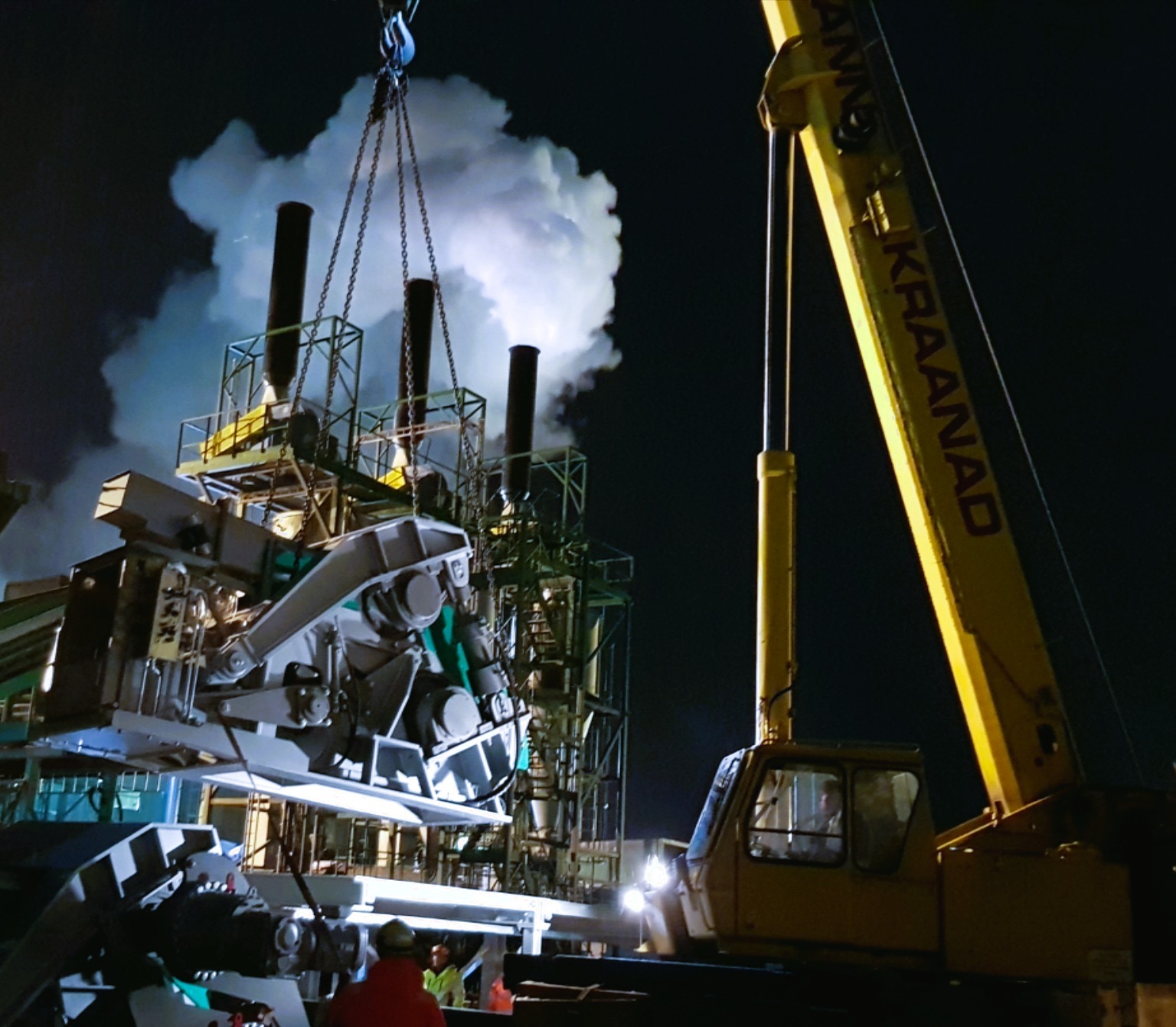
Dold Holzwerke GmbH
A traditional company from the Black Forest. In order to make the production process for pellet production more energy efficient, two parallel wood chip crushers including water treatment were installed.
Neuson Hydrotec
since 1981
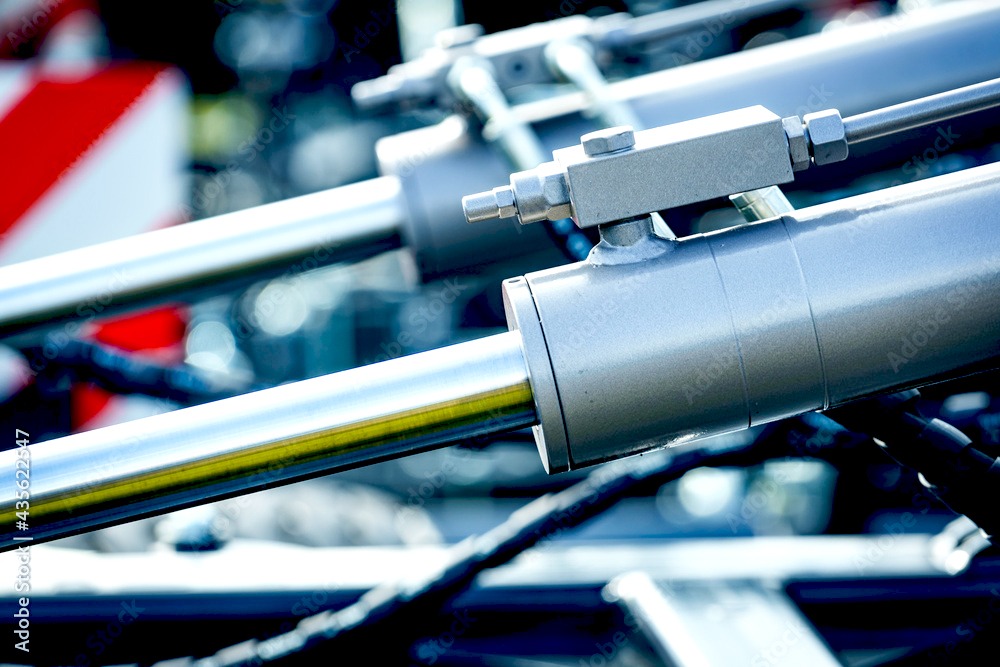
Example Title 1
Lorem ipsum dolor sit amet, consectetur adipiscing elit. Mauris tempus nisl vitae magna pulvinar laoreet.
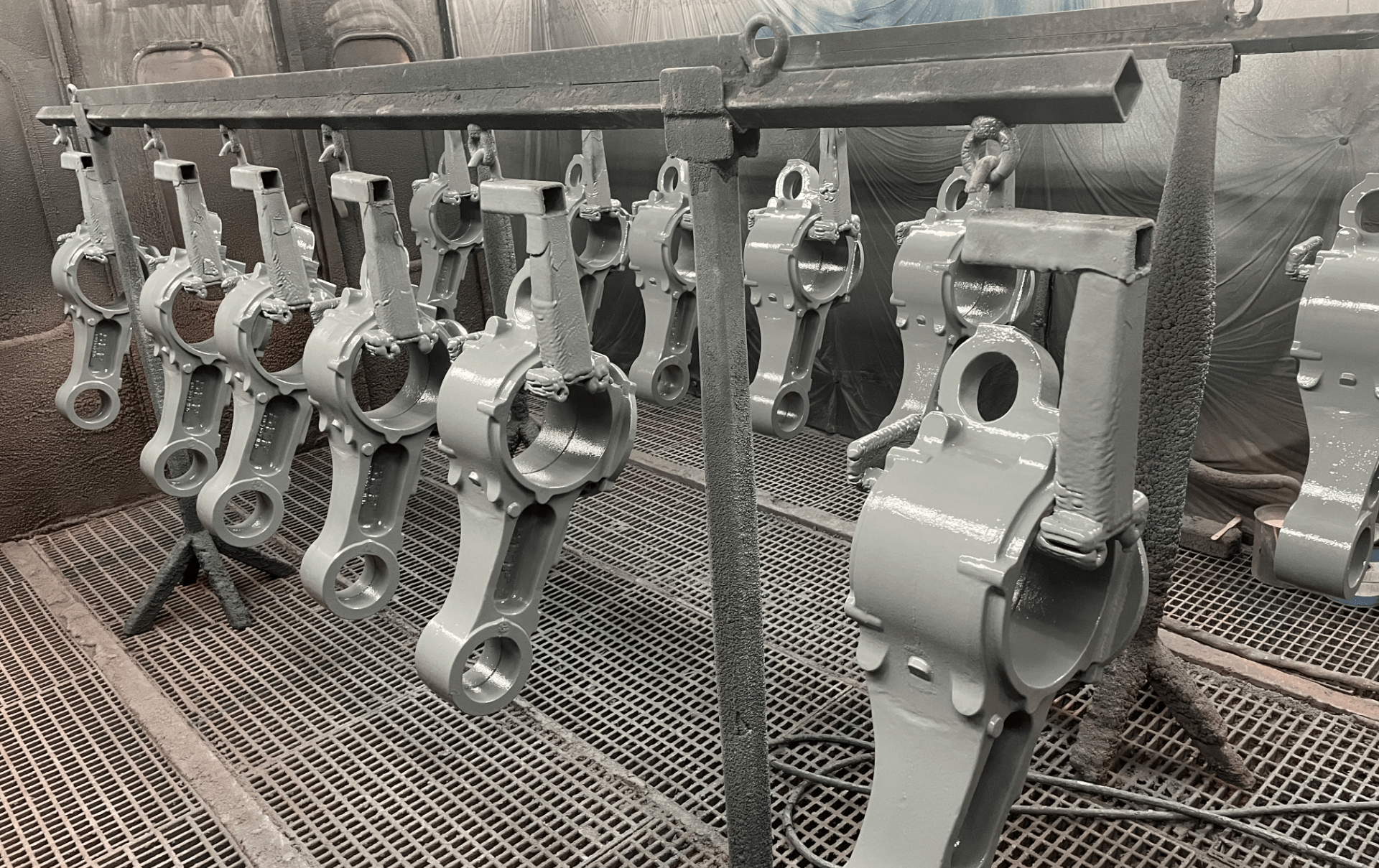
Example Title 2
Lorem ipsum dolor sit amet, consectetur adipiscing elit. Mauris tempus nisl vitae magna pulvinar laoreet.
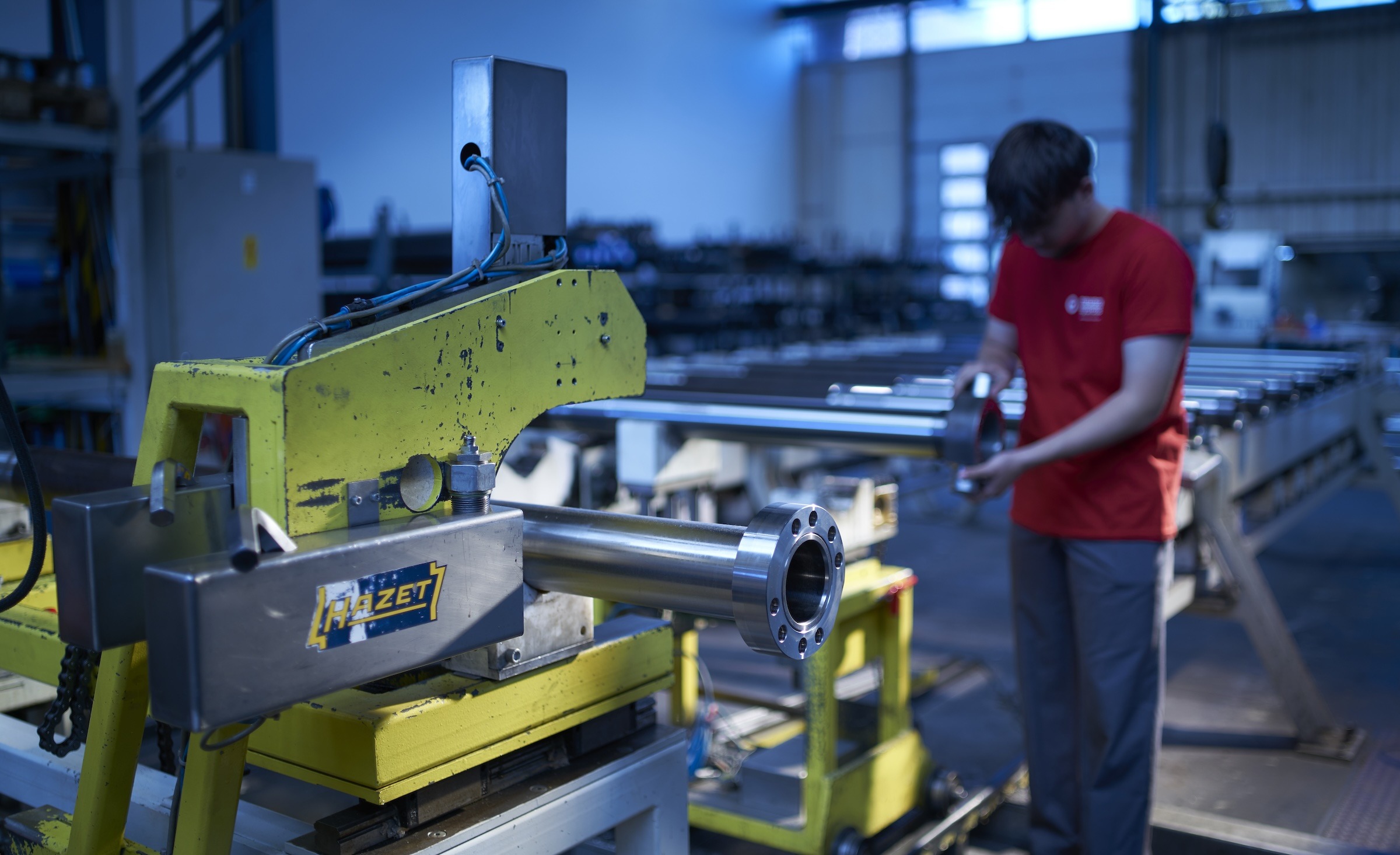
Example Title 3
Lorem ipsum dolor sit amet, consectetur adipiscing elit. Mauris tempus nisl vitae magna pulvinar laoreet.
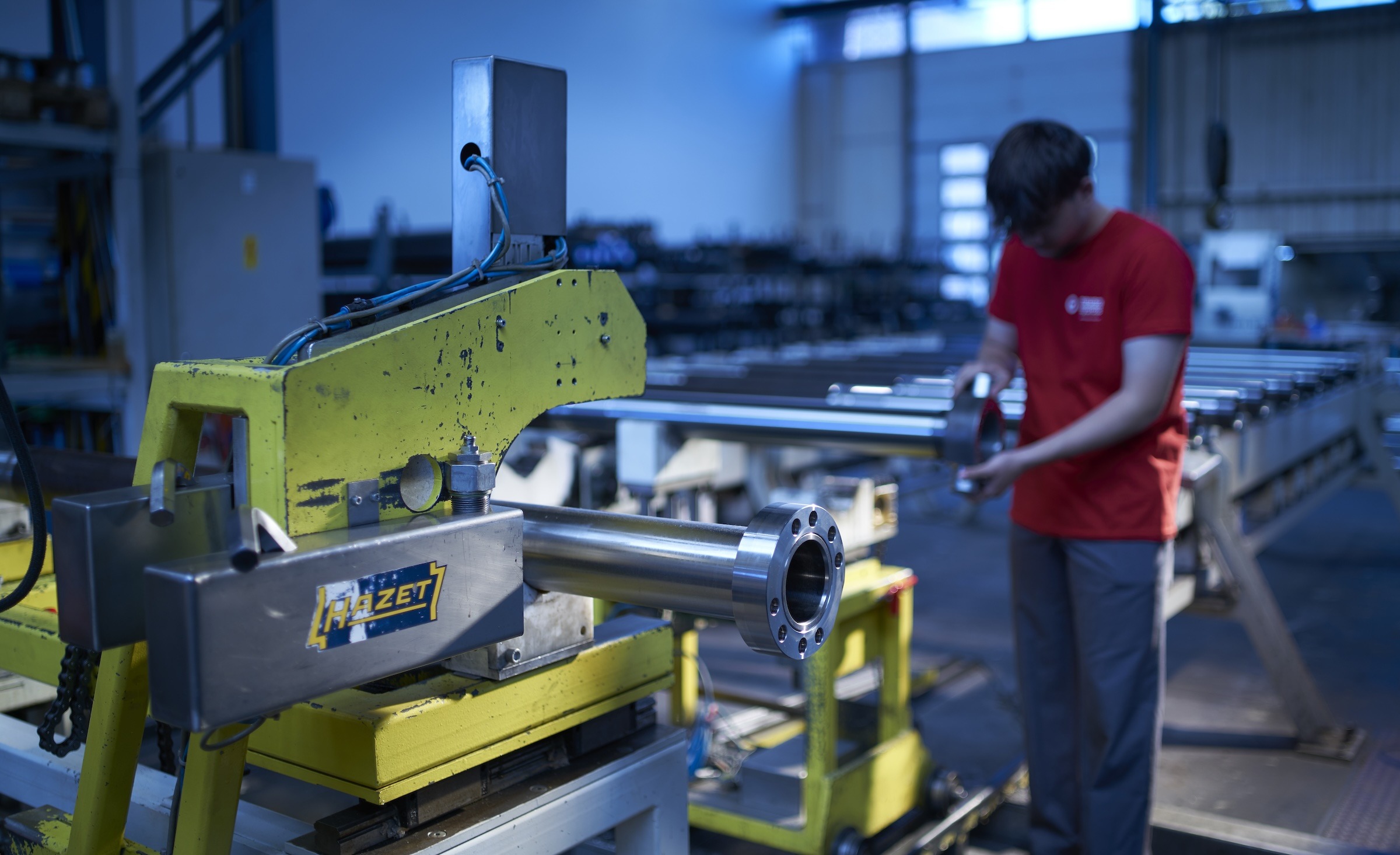
Example Title 3
Lorem ipsum dolor sit amet, consectetur adipiscing elit. Mauris tempus nisl vitae magna pulvinar laoreet.
See our solutions in action
Book an appointment with our experts to discuss your requirements and gain an insight into our innovative solutions.
Success stories
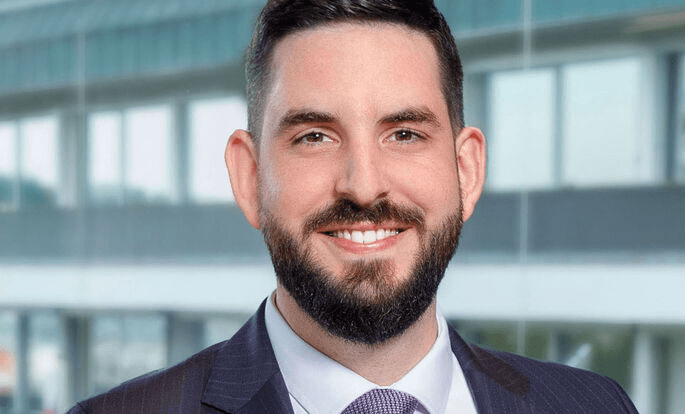
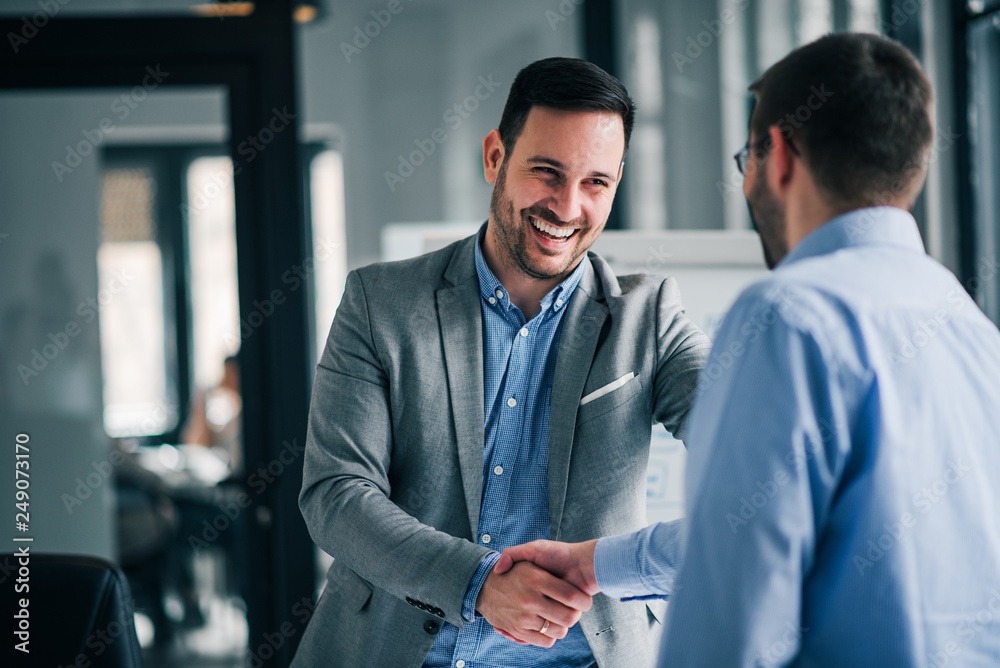
Functional principle:
As with wringing out a wet towel, most of the water is removed from the fabric using mechanical energy. This means that the roller press can also remove around half of the water from the wood chips with very little energy input. It can then be used as fuel or for further processing.
The core element is the patented conveyor chain, which runs between two large rollers. The chain rests on the lower roller and is driven by friction. It conveys the wood chips into the pressing zone. In the pressing zone, it forms an almost closed pressing surface on one side – the other side is the upper pressing roller. At the same time, the chain offers optimum dewatering through narrow gaps between the chain links packed on top of each other, so that the water can disappear directly in the pressing zone, i.e. at maximum pressure. This must be the case because the pressed wood chips would immediately reabsorb at least part of the water when the pressure is released. The rollers are pressed together hydraulically with a pressing force of around 100 tons over a width of 50 cm.
The chain is deflected several times after pressing. This opens the gaps between the chain links and the chain cleans itself. The press is designed for 24/7 operation. The robust design combines low-wear operation with low drive power. The current systems have now completed thousands of operating hours and show no signs of unforeseen wear.
Contact us to plan your individual machine.
From the sketch to the finished machine – Neuson Hydrotec offers modular systems for the highest demands in the wood and steel industry, as well as in the field of renewable energies.
FAQs
For mechanical drying of wood chips and wood waste to remove the dissolved water. This enables a continuous supply of material for the downstream belt dryer.
Yes! With around one kilowatt hour of mechanical energy, more than 70 liters of water are pressed out of the wood chips. Conventional systems with classic hot air drying require 1.7 kWh electrically and 90 kWh thermally.
This significant improvement in the energy balance results in considerable savings compared to conventional thermal drying processes. A large proportion of the free water that is not bound in the cell wall is removed mechanically. This makes the entire drying process more efficient and economical compared to conventional thermal processes. This results in further potential savings in drying costs.
Yes!
The resulting press water (approx. 1-2 m³/h) contains minerals and organic components. These are then flushed out of the wood, which brings important advantages in the event of subsequent combustion: the proportion of mineral residues in the crushed wood chips is significantly reduced. This reduces the amount of ash and, in particular, the amount of fine dust in the exhaust gas. The systems operated with the pressed wood chips have a considerably reduced ash accumulation and fewer deposits in the combustion chamber.
The savings potential due to the reduced water content in direct combustion is around 10-12%, according to previous experience. If the improved system efficiency is taken into account, experience has shown that fuel savings of 15-20% can be achieved.
Around half the weight of freshly harvested softwood consists of water. This water impairs the storability (rotting, mold growth) and reduces the calorific value.
An almost completely dry wood raw material is required for further processing into chipboard or pellets. Technical drying is essential here, usually using large, continuously operated belt dryers. There, the wood chips pass through a hot air stream on an air-permeable conveyor belt. The belt runs more slowly for particularly wet woodchippings and faster for pre-dried woodchippings. In practice, the hot air is often generated using natural gas or, depending on availability, with the help of process heat available on site.
The wood chips should also have a certain degree of dryness for combustion in order to achieve optimum combustion. If the wood chips are very moist, an unnecessarily large proportion of the thermal energy is consumed for the evaporation of the water alone. For this reason, a drying process is almost always installed upstream of wood chip combustion systems. Drying is often carried out by storing the woodchippings for a longer period of time, whereby microbial activity heats up and dries the pile. However, this type of drying results in a significant loss of calorific value.
There is another good reason for crushing woodchippings directly at the sawmill: if half of the water disappears directly at the mill, a quarter of the weight of the woodchippings also disappears – and a superfluous quarter at that. This immediately saves transportation costs. In practice, this means that the usual large-capacity trucks can be fully loaded with pressed wood chips. With naturally moist woodchippings, a maximum of 80% of the filling quantity can generally be loaded – after that there is a risk of overloading. Experience to date has shown that between 20% and 25% of the transportation costs are eliminated during onward transport.
A dew system was developed to ensure stable year-round operation. It can be fed from the waste heat of the biomass power plant. The circulation of the (deep) frozen wood chips in a counter-current process and the screw conveyors used have proven themselves in everyday operation.
Special machine construction
Wood chip press
Your contact for special machines
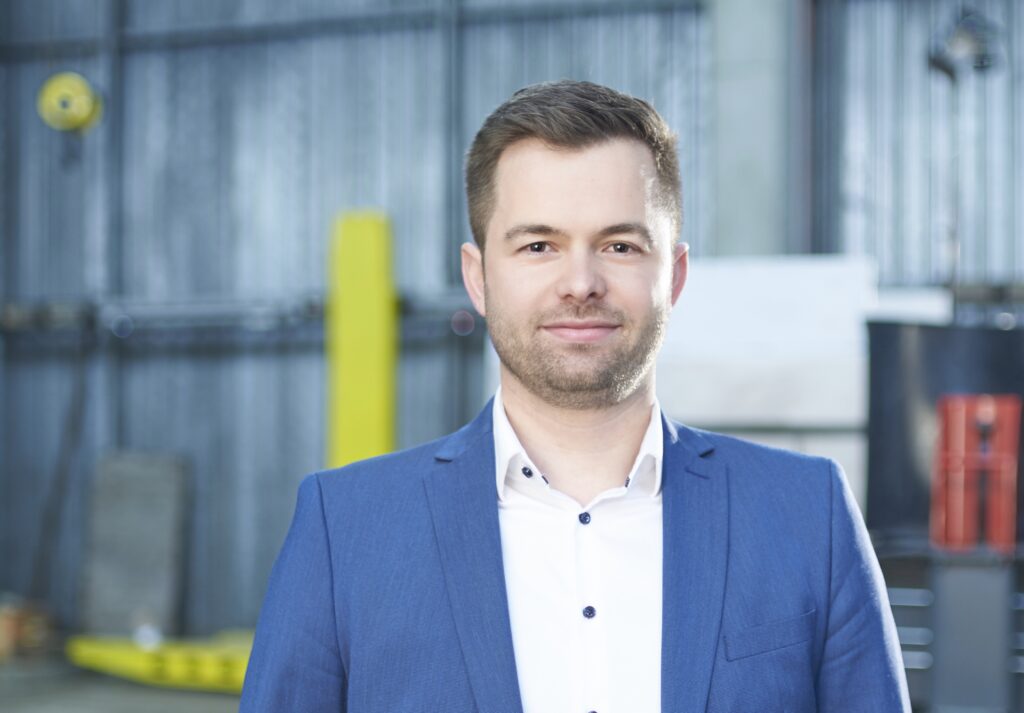
Matthew Kramer
Head of special machine construction
“With the right system, you can also increase your business potential. Take advantage of our technical knowledge, expand your resources with our products and benefit economically from the collaboration. Discuss the most economical solution for your machines and systems with us.”
Your sales contact
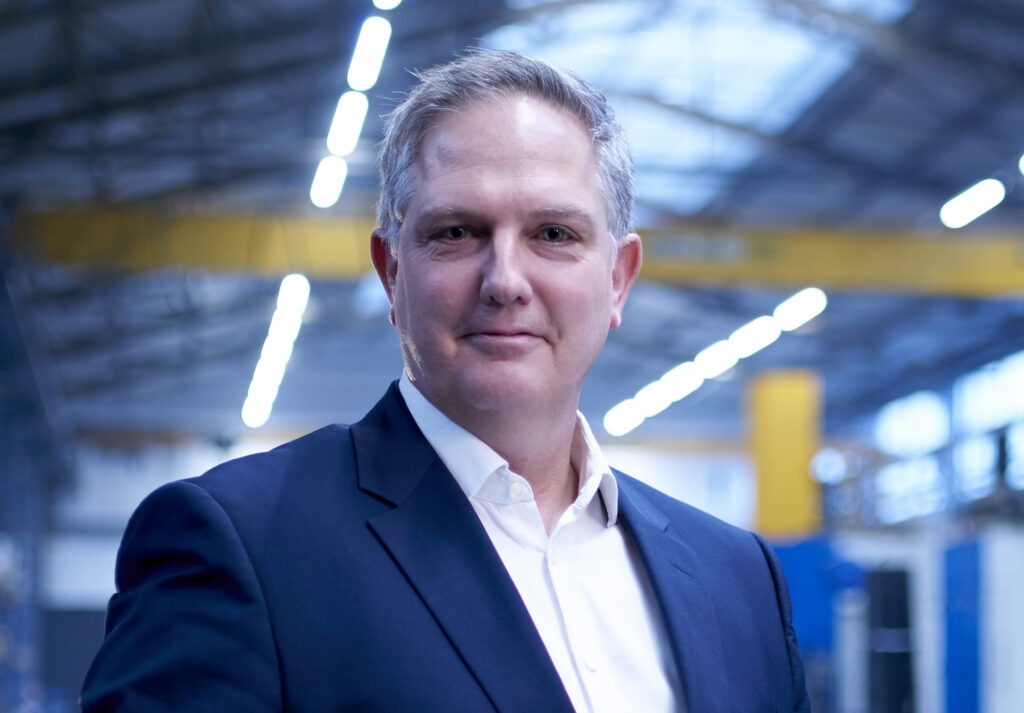
Robert Blauhut
Managing Director
“We actively motivate our clients to involve us even earlier in the development of systems, components and machines in future. Because one thing is clear in all areas of expertise: our product solutions become more specific, more economical and more pioneering the earlier we contribute know-how, industry experience and creative solution expertise. This is how we leverage synergies at the interfaces of hydraulics, mechanical engineering and electronics for greater visibility on the market. For us and for our clients!”
Your customer service contact
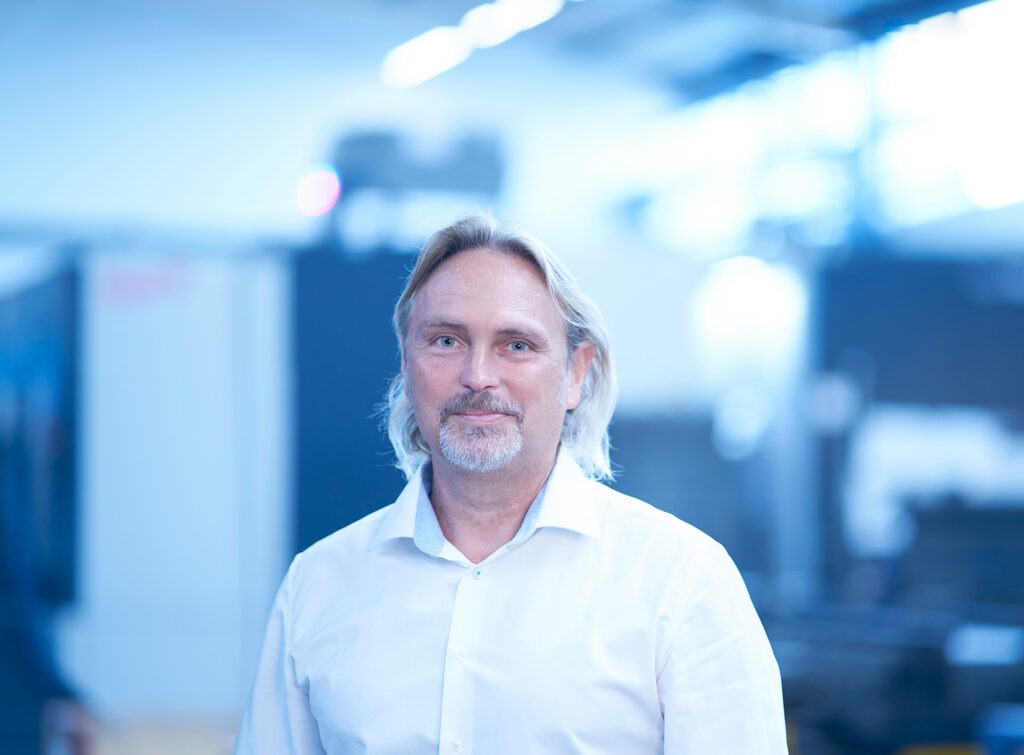
Jürgen Grammer
Customer service & Aftersales
“The purchase of special machines from Neuson Hydrotec is not the end of a sales process, but the beginning of a responsible relationship with our customers. With the Service Center, we offer comprehensive maintenance and repair services as well as a huge selection of spare parts for Neuson components and certified commercial products to anyone who appreciates good service.”